Контактное формование: проблемы и решения
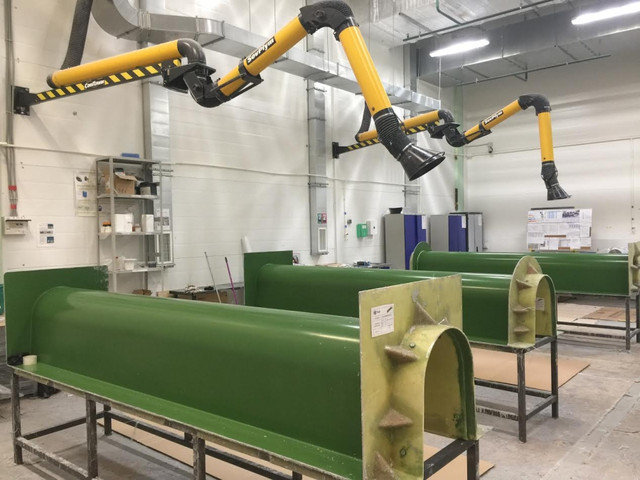
При создании многослойного пластика методом контактного формования хорошее соединение смолы и армирующего материала играют важнейшую роль, определяющую свойства конечного изделия. Мы остановимся на важнейших этапах, определяющих качество изделий: Равномерное распределение смолы Необходимо следить за хорошим распределением смолы при нанесении ее с помощью распылительного оборудования, кисти или валика. Зоны изделия, обедненные смолой при формовании, в последствие являются наиболее слабыми местами. Зоны же чрезмерно обогащенные смолой сильно разогреваются в процессе отверждения, деформируются и растрескиваются. Конечное изделие может быть хрупким. Равномерное распределение армирующего материала Полученный результат сильно зависит от оператора или формовщика. Среди существующих видов армирующих материалов наибольшую неравномерность имеют армирующие материалы в виде мата. Масса в рулоне может варьироваться на +/- 10%. Для гарантированно хорошего результата предпочтительно использовать ткани, сетки или ровинговые ткани. Соотношение смола/стекло Не только распределение смолы, но также и процентное содержание армирующего материала определяют появление или отсутствие зон непропитанных смолой или содержащих чрезмерное её количество. Уточняйте процентное содержание армирующего материала для минимизации возможных проблем. Уменьшение воздушных пузырей Невозможно ликвидировать все возможные пузырьки, когда мы используем технологию контактного формования. Но процесс последующего удаления воздуха, путем тщательной прикатки, позволил бы ограничить их размер и количество. Пузыри крупного размера делают смолу светлой, белесой. Если зона поражения критична и расположена прямо за слоем гелькоута рекомендуется использовать для первого слоя тонкий мат или напылять тонкий слой ровинга. Количество пузырей или маленьких кратеров в верхних слоях ламината и на поверхности также должно регулироваться тщательным процессом удаления пузырей. Влияние температуры Так как полимеризация смолы сопровождается выделением тепла важно контролировать эту реакцию. Для этого используйте минимально возможное количество катализатора (отвердителя), изготавливайте немного слоев за один подход и дождитесь их остывания перед изготовлением следующих. Избегайте зон чрезмерного скопления смолы. Для изготовления толстого ламината (более 3 мм) выбирайте смолы с пониженным экзотермическим пиком. Для сохранения долговечности используемой матрицы температура разогрева изделия не должна превышать 60°С. Контроль риска расслоения Этот феномен (разделение двух или более слоев в ламинате) может происходить из-за того, что соединение и уплотнение слоев было проведено не тщательно. Для исключения этого риска чередуйте слой мата со слоями холстов или ровинговых тканей. Архитектура волокон в мате позволяет соединять эти слои наиболее продуктивно и также увеличивает стойкость к сдвиговым нагрузкам. Слоистый пластик составляет наибольшую часть всех изделий из стеклопластика. Безусловно, именно слоистая структура придает изделию прекрасные механические свойства. Но не только дефекты в ламинате делают изделие бракованным, зачастую и поверхность гелькоута может повлиять на конечный результат. Если пленка гелькоута слишком тонка, то она не сможет ни компенсировать, ни скрыть дефекты ламината. Также появления расслоения можно ожидать в том случае, когда перерывы между формованием слоя гелькоута и ламината, либо между слоями ламината слишком длительные. Контактное формование - проблемы, причины, решения. Проблемы: Изменение цвета в ламинате Причины: Ламинирование под действием нагрева Решения или предупреждение: Хорошо перемешивайте катализатор;
Снизьте количество катализатора;
Имеются зоны слишком обогащенные смолой;
Влажный армирующий материал.
Проблемы: Время отверждения слишком короткое или длинное Причины: Различные Решения или предупреждение: Контролируйте величество и тип катализатора, температуру, толщину ламината, время гелеобразования, наличие загрязнений. Проблемы: Расслоение: Между слоем гелькоута и ламинатом
Между слоями ламината
Причины: Загрязнение
Недостаточное или чрезмерное отверждение.
Создание слоев
Смола
Слои ткани вплотную друг к другу
Нет отверждения.
Решения или предупреждение: Пыль на гелькоуте
Накопление разделительных материалов на гелькоуте
Использование продуктов чистовой отделки вместо гелькоута
Время осуществления гелькоута перепроверить
Плохое пропитывание или зоны с чрезмерным количеством смолы.
Воск в смоле
Недостаточное отверждение смолы: перепроверить качество и физические характеристики. Используйте мат или резаное стекло между слоями ткани.
Проверьте количество катализатора, температуру, время расформовки.
Проблемы: Маленькие кратеры в гелькоуте Причины: Частицы в ламинате Решения или предупреждение: Контролируйте связывание мата (с двух сторон: с одной стороны он может быть более наполненным, чем с другой);
Возможное присутствие грязи или пыли между гелькоутом и ламинатом, или частички в смоле
Проблемы: Пропитывание: Армирующий слой не сухой
Армирующий слой сухой
Причины: Чрезмерное количество смолы
Тонкий слой смолы
Время гелеобразования очень длинное
Решения или предупреждение: Низкое соотношение смолы по сравнению с армирующим материалом; избегайте дополнительного смачивания смолой между слоями.
Используйте смолу с большой вязкостью
Увеличьте количество катализатора, ориентируясь на разрешенный лимит, контролируйте температуру
Проблемы: Время гелеобразования очень длинное или очень короткое Причины: Различные Решения или предупреждение: Обратите внимание на процент и тип катализатора, температуру, толщину ламината, заявленное время гелеобразования, присутствие загрязнений Проблемы: Гофрирование и волнистость в гелькоуте Во время расформовки
После расформовки
Причины: Усадка смолы или чрезмерный разогрев
Недостаточная толщина гелькоута.
Гелькоут недостаточно отвержден.
Процесс ламинирования
Решения или предупреждение: Проверьте количество катализатора и температуру; используйте смолу с меньшим экзотермическим пиком; избегайте скопления смолы.
Гелькоут может быть слишком текучей или недостаточно отвержден.
Наносите гелькоут слоем не менее 0,45 мм Используйте не менее 1,2% МЕКР; температура при нанесении гелькоута - не менее 20С
Большая толщина за один раз (используйте скин слой): ровинговая ткань или полотно слишком близко к слою гелькоута.
Количество катализатора слишком низкое; температура слишком низкая; примеси в смоле
Экзотерма смолы не достаточно высокая;
Преждевременная расформовка;
Слой гелькоута слишком мал.
Проблемы: Стекло приклеивается к валику Причины: Прохождение валиком по зоне, где началась желатинизация смолы
Испарение стирола
Слишком быстрое движение валика
Количество стекла слишком велико
Валики загрязнены
Решения или предупреждение: Подстраивайтесь под время гелеобразования.
Быстрое намокание ролика в стироле или в катализированной смоле
Ограничивать, насколько возможно, движение воздуха в ламинате
Пересмотрите метод ламинирования
Увеличьте количество смолы
Смените растворитель
Проблемы: Трещина в смоле Причины: Преждевременная расформовка
Перегрев
Решения или предупреждение: Не расформовывайте недостаточно отвержденные изделия
Скопления смолы: много катализатора, экзотерма смолы слишком высока.
Проблемы: Мягкие зоны в изделии Причины: Катализатор плохо перемешан
Вода, растворитель или масло
Решения или предупреждение: Контролируйте оборудование подачи, смешивания смолы и катализатора (пробки, разница в давлении, утечка).
Контролируйте чистоту шлангов для подачи смолы/катализатора и валиков
Проблемы: Пузыри, пустоты Причины: Скопление воздуха Решения или предупреждение: Процесс обезвоздушивания проведен плохо;
Медленная пропитка армирующего материала;
Зоны, плохо пропитанные смолой,
Слишком вязкая смола.
Проблемы: Деформация изделия Причины: Ламинат плохо откалиброван Решения или предупреждение: Используйте армирующий материал симметрично;
Наносите гелькоут либо материал для финишной обработки на обратную сторону изделия.
Снизьте количество катализатора;
Имеются зоны слишком обогащенные смолой;
Влажный армирующий материал.
Проблемы: Время отверждения слишком короткое или длинное Причины: Различные Решения или предупреждение: Контролируйте величество и тип катализатора, температуру, толщину ламината, время гелеобразования, наличие загрязнений. Проблемы: Расслоение: Между слоем гелькоута и ламинатом
Между слоями ламината
Причины: Загрязнение
Недостаточное или чрезмерное отверждение.
Создание слоев
Смола
Слои ткани вплотную друг к другу
Нет отверждения.
Решения или предупреждение: Пыль на гелькоуте
Накопление разделительных материалов на гелькоуте
Использование продуктов чистовой отделки вместо гелькоута
Время осуществления гелькоута перепроверить
Плохое пропитывание или зоны с чрезмерным количеством смолы.
Воск в смоле
Недостаточное отверждение смолы: перепроверить качество и физические характеристики. Используйте мат или резаное стекло между слоями ткани.
Проверьте количество катализатора, температуру, время расформовки.
Проблемы: Маленькие кратеры в гелькоуте Причины: Частицы в ламинате Решения или предупреждение: Контролируйте связывание мата (с двух сторон: с одной стороны он может быть более наполненным, чем с другой);
Возможное присутствие грязи или пыли между гелькоутом и ламинатом, или частички в смоле
Проблемы: Пропитывание: Армирующий слой не сухой
Армирующий слой сухой
Причины: Чрезмерное количество смолы
Тонкий слой смолы
Время гелеобразования очень длинное
Решения или предупреждение: Низкое соотношение смолы по сравнению с армирующим материалом; избегайте дополнительного смачивания смолой между слоями.
Используйте смолу с большой вязкостью
Увеличьте количество катализатора, ориентируясь на разрешенный лимит, контролируйте температуру
Проблемы: Время гелеобразования очень длинное или очень короткое Причины: Различные Решения или предупреждение: Обратите внимание на процент и тип катализатора, температуру, толщину ламината, заявленное время гелеобразования, присутствие загрязнений Проблемы: Гофрирование и волнистость в гелькоуте Во время расформовки
После расформовки
Причины: Усадка смолы или чрезмерный разогрев
Недостаточная толщина гелькоута.
Гелькоут недостаточно отвержден.
Процесс ламинирования
Решения или предупреждение: Проверьте количество катализатора и температуру; используйте смолу с меньшим экзотермическим пиком; избегайте скопления смолы.
Гелькоут может быть слишком текучей или недостаточно отвержден.
Наносите гелькоут слоем не менее 0,45 мм Используйте не менее 1,2% МЕКР; температура при нанесении гелькоута - не менее 20С
Большая толщина за один раз (используйте скин слой): ровинговая ткань или полотно слишком близко к слою гелькоута.
Количество катализатора слишком низкое; температура слишком низкая; примеси в смоле
Экзотерма смолы не достаточно высокая;
Преждевременная расформовка;
Слой гелькоута слишком мал.
Проблемы: Стекло приклеивается к валику Причины: Прохождение валиком по зоне, где началась желатинизация смолы
Испарение стирола
Слишком быстрое движение валика
Количество стекла слишком велико
Валики загрязнены
Решения или предупреждение: Подстраивайтесь под время гелеобразования.
Быстрое намокание ролика в стироле или в катализированной смоле
Ограничивать, насколько возможно, движение воздуха в ламинате
Пересмотрите метод ламинирования
Увеличьте количество смолы
Смените растворитель
Проблемы: Трещина в смоле Причины: Преждевременная расформовка
Перегрев
Решения или предупреждение: Не расформовывайте недостаточно отвержденные изделия
Скопления смолы: много катализатора, экзотерма смолы слишком высока.
Проблемы: Мягкие зоны в изделии Причины: Катализатор плохо перемешан
Вода, растворитель или масло
Решения или предупреждение: Контролируйте оборудование подачи, смешивания смолы и катализатора (пробки, разница в давлении, утечка).
Контролируйте чистоту шлангов для подачи смолы/катализатора и валиков
Проблемы: Пузыри, пустоты Причины: Скопление воздуха Решения или предупреждение: Процесс обезвоздушивания проведен плохо;
Медленная пропитка армирующего материала;
Зоны, плохо пропитанные смолой,
Слишком вязкая смола.
Проблемы: Деформация изделия Причины: Ламинат плохо откалиброван Решения или предупреждение: Используйте армирующий материал симметрично;
Наносите гелькоут либо материал для финишной обработки на обратную сторону изделия.
Другие статьи
- Виды искусственного камняКраткий обзор на тему, чем отличаются разные виды искусственного камня и из каких составляющих изготавливаются.Полная версия статьи